wandersen
Well-Known Member
- Joined
- Jul 31, 2007
- Messages
- 519
- Reaction score
- 140
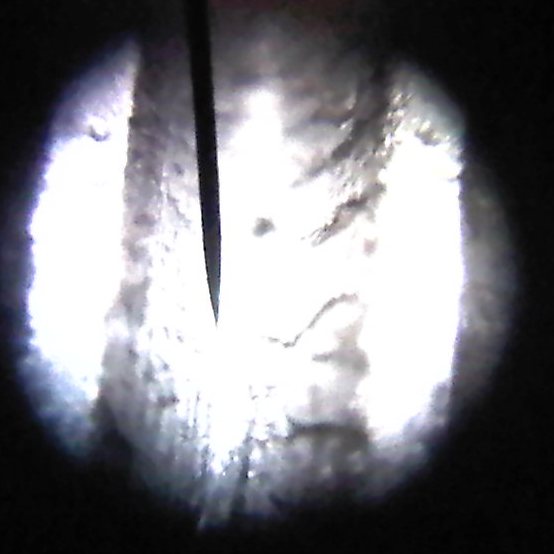
I'm working on cutting threads on my drag/anti-drag wires. I'm having problems getting a good surface finish on the 4130 thread grooves. On 304 stainless rod, I get a very smooth and very acceptable thread finish.
My preference is to cut the 1/4"and 3/16" drag/anti-drag wires out of 4130 due to almost double the yield strength.
I'm cutting the threads on a mini lathe with HSS cutting tool with a standard 60 deg cutting head. I'm cutting the threads at an offset of 29 degree feed angle. I ordered the 1/4" and 3/16" 4130 rod from spruce. I've tried cutting as high as 100 sfm (really hard to do) and cut at at dead slow speeds. I've cut dry and cut lubricated. I've changed angles on the cutting tool, cut with a strait tool, cut with a low angle tool (hooked end). No matter what I do, I get micro fissures or micro tears in the 60 deg angle surfaces perpendicular to the cutting direction. When cutting, the chips are coming off nicely in long curly chips . I've tried feeding at more than 0.005" cuts. I've tried feeding at 0.001". This doesn't seem to effect the surface finish all that much. I get the same result on the 1/4" or the 3/16" rod. As a test, I tried running threads on 4130 tube and go the same micro fissures.
When I cut threads on 304 stainless rod, they are clean as a whistle.
I haven't tried a carbide cutting tool.
Is there a way to cut better threads on 4130 rod?
I'm viewing the threads on a 40 power scope.
Edited by: wandersen